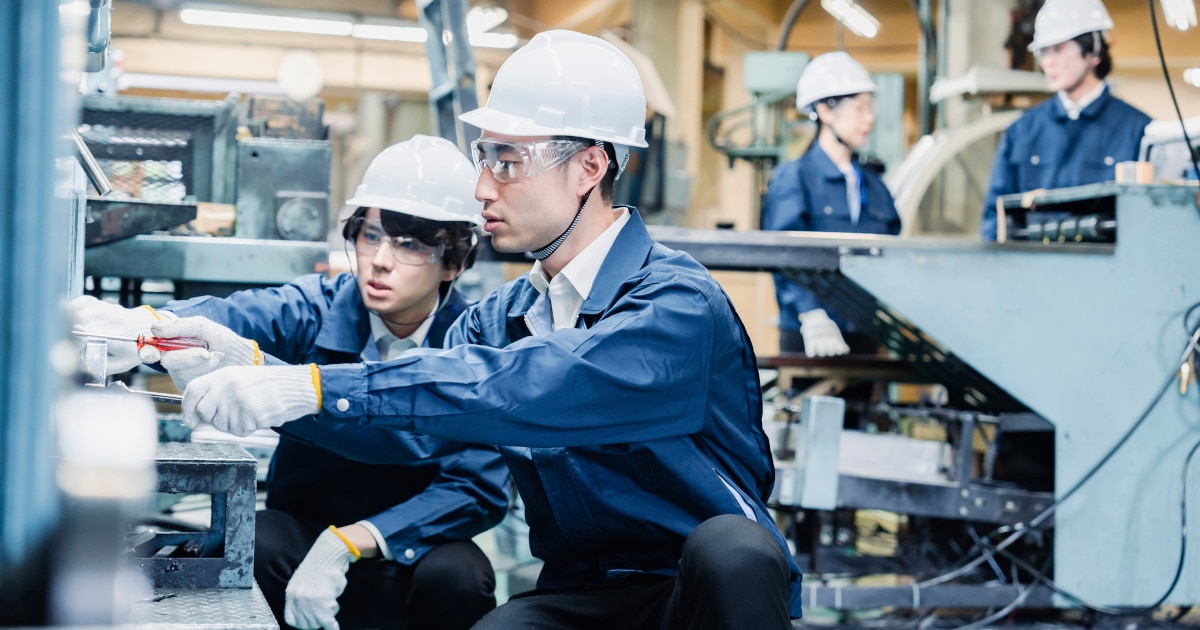
歩留まりを改善する4つの方法。考えられる原因や取り組むポイントを解説
製造業において、製品の収益性や生産の効率性を把握するために重要な指標となるのが“歩留まり”です。歩留まりとは、投入した原材料によって生産された製品に対して良品が占める割合を指します。
歩留まりが高くなるほど、原材料のロスや製品の不良率が低く、効率的に生産を行えている状態となります。一方、歩留まりが低い場合には、製品開発の計画や製造プロセスなどに何らかの問題があると考えられます。
製造コストの増加を防いで収益性や生産性の向上を図るには、歩留まりが低くなる原因を知り改善に取り組むことが重要です。
この記事では、歩留まりが低下する主な原因と4つの改善方法、取り組みのポイントについて解説します。
目次[非表示]
- 1.歩留まりが低下する主な原因
- 2.歩留まりを改善する4つの方法
- 2.1.➀従業員の教育によるスキルの向上
- 2.2.②製造プロセスの見直し
- 2.3.③メンテナンス周期の最適化
- 2.4.④品質管理の強化
- 3.歩留まりの改善に取り組むポイント
- 4.まとめ
歩留まりが低下する主な原因
歩留まりが低いと、製造にかかったコストに対して期待される完成品の数が少ない状態となり、生産効率の低下と収益の悪化につながります。歩留まりが低下する原因には一般的に以下のような項目が挙げられます。
▼歩留まりが低下する主な原因
- 原材料の不良または過剰仕入れ
- 設備・機械トラブルによる生産停止
- ヒューマンエラー
- 製品設計段階での見積りミス など
原材料に不良や不純物の混入があったり、過剰な仕入れによって品質保持期間が過ぎたりすると、調達にかかったコストを回収できず廃棄ロスを招きます。また、設備・機械に不具合や故障が起きることで、品質不良の発生、生産ラインの停止が起きて歩留まりが低下することもあります。
さらに、製造担当者が作業手順を間違えたり、原材料の投入量や機械の条件設定を誤ったりするヒューマンエラーが起きた場合にも、品質不良の発生、原材料の廃棄ロスにつながります。そのほか、製品の設計段階で設定した歩留まりの見積りが実態と合わず、結果的に歩留まりが低くなるケースも考えられます。
歩留まりを改善する4つの方法
歩留まりの改善を図るには、製造プロセスと品質管理の体制を見直して、ヒューマンエラーや設備・機械のトラブルを防ぐことが重要です。
➀従業員の教育によるスキルの向上
ヒューマンエラーによって製品や原材料の不良が発生している場合には、従業員に教育を実施してスキルを強化する方法があります。
作業の習熟度に問題がある従業員に教育を実施することで、スキルの均一化と作業精度の向上を図れます。
▼従業員の教育方法
- 熟練技術者によるOJT
- 外部の事業者による研修・講習
- 作業習熟度を測るテストの実施とフィードバック
- 作業手順書のペーパーレス化による業務標準化 など
②製造プロセスの見直し
現状の製造プロセスを洗い出して、歩留まりの低下を招いているフローや作業内容を見直すことも方法の一つです。
製造プロセスの各段階で歩留まりを算出して問題点を明らかにすることで、改善に向けた具体的な施策を検討できます。
▼製造プロセスの改善例
取り組み |
具体例 |
製造工数の削減 |
|
作業工程の標準化 |
|
設備・機械の管理 |
|
データの収集・分析 |
|
設計段階において、部品点数や加工工程、工法などを見直してトータルの製造工数を減らすことで、製造原価の低減を図れます。この製品開発プロセスの初期段階である設計・開発において、リソースを投下することをフロントローディングと呼びます。これにより収益性が向上して歩留まりの改善が期待できます。
人の手で行う業務については、作業手順やマニュアルを策定して担当者ごとに対応のばらつきが生まれないようにすることが必要です。
また、IoTやAI、システムを活用すると設備・機械の稼働状況を可視化でき、遠隔での制御とデータの一元管理が可能になります。これにより、作業の一部を自動化・省人化してヒューマンエラーを防いだり、データ分析によって歩留まりが低下する原因を特定したりできます。
■不良要因究明に役立つデータ解析アプローチ方法はこちら
③メンテナンス周期の最適化
設備・機械のトラブルによって生産停止や不良の発生を招いている場合には、メンテナンス周期を見直すことも方法の一つです。
製造業での保全活動において、設備・機械が故障する前に行うメンテナンスの方法には“予防保全”と“予知保全”の2つがあります。
▼予防保全と予知保全の仕組み
予防保全 |
予知保全 |
|
仕組み |
定期的な点検を実施して、部品交換や補修を行う |
センサーやPLCで稼働データを取得して、故障の予兆が見られる際に保全を行う |
メンテナンスのタイミング |
一定期間が経過したとき、または設備の劣化や異常の兆候が見られたとき |
異常の予兆を検知したとき |
予防保全を採用しており、故障・不具合が発生する頻度が多い場合には、点検箇所やメンテナンスの頻度を増やして保守計画を見直すことが重要です。ただし、過剰なメンテナンスは、保守点検のコスト増大や一時停止による生産ロスを招いてしまいます。
歩留まりを改善するには、IoTやAIの活用によって設備・機械の稼働状況を常時監視して、故障の予兆検知を行える仕組みを構築することが有効です。予知保全を実現することで、メンテナンス頻度を最適化して保守点検コストを削減できるほか、突発的な設備停止の防止につながります。
なお、設備管理のポイントについてはこちらの記事で解説しています。
④品質管理の強化
歩留まりを改善するには、製造プロセスでの品質管理を強化して原材料と製品の不良率を減らすことが必要です。
設備・機械の点検作業や製品検査の方法を標準化したり、不良が頻繁に起きる部品を見直したりする方法があります。ただし、目視による点検・品質検査では、担当者ごとに作業精度のばらつきが生じたり、チェック漏れや勘違いなどによるヒューマンエラーが生じたりする可能性があります。
品質管理の強化を図るには、IoTやAI、システムなどのデジタル技術を活用することが有効です。
▼デジタル技術を活用した品質管理の例
- 設備・機械の遠隔制御による条件設定
- センサーやカメラによる投入量・温度・湿度などの自動計測
- IoTやシステムの活用による目視点検の自動化
- 自動外観検査装置の導入 など
また、生産実績や不良の発生履歴、設備・機械の点検記録などのデータをシステム上に蓄積すると、製造部門・設計部門・保全部門でのリアルタイムな情報共有が可能になり、品質の安定化に取り組めます。
なお、品質管理を効率化するポイントについては、こちらの記事で解説しています。併せてご確認ください。
歩留まりの改善に取り組むポイント
歩留まりの改善に取り組む際は、製造プロセスのどの工程に問題があるか原因を調査・特定することがポイントです。
不良の発生原因を分析する際に必要となる視点に“5M+1E”があります。
▼品質管理における5M+1E
項目 |
主な分析項目 |
人(Man) |
|
設備・機械(Machine) |
|
原材料(Material) |
|
方法(Method) |
|
測定・検査(Measurement) |
|
環境(Environment) |
|
5M+1Eの視点で品質管理の項目と基準を設定することで、“製造工程でいつもと異なる点”“正常とは異なる動きや環境”などが明らかになり、不良の発生原因を特定できる場合があります。
また、原因を踏まえて歩留まりの改善策を講じたあとは、定期的にデータの分析と評価を行い改善のサイクルを回すことも重要です。
まとめ
この記事では、歩留まりについて以下の内容を解説しました。
- 歩留まりが低下する主な原因
- 歩留まりを改善する4つの方法
- 歩留まりの改善に取り組むポイント
歩留まりが低下すると、製造コストの増大や生産性の低下を招き、経営状態にも影響を及ぼします。効率的な生産体制を構築して収益性を高めるためには、不良率の低減や製造プロセスの最適化を図り、歩留まりの改善に取り組むことが重要です。
『アットフィールズテクノロジー』では、IoT・システムの活用によって製造プロセスの改善や品質管理を行えるソリューションを提供しております。システム環境の構築からデータ解析による課題抽出まで、高品質かつ高効率な生産体制を実現するためのサポートを行います。
詳しくは、こちらの資料をご確認ください。