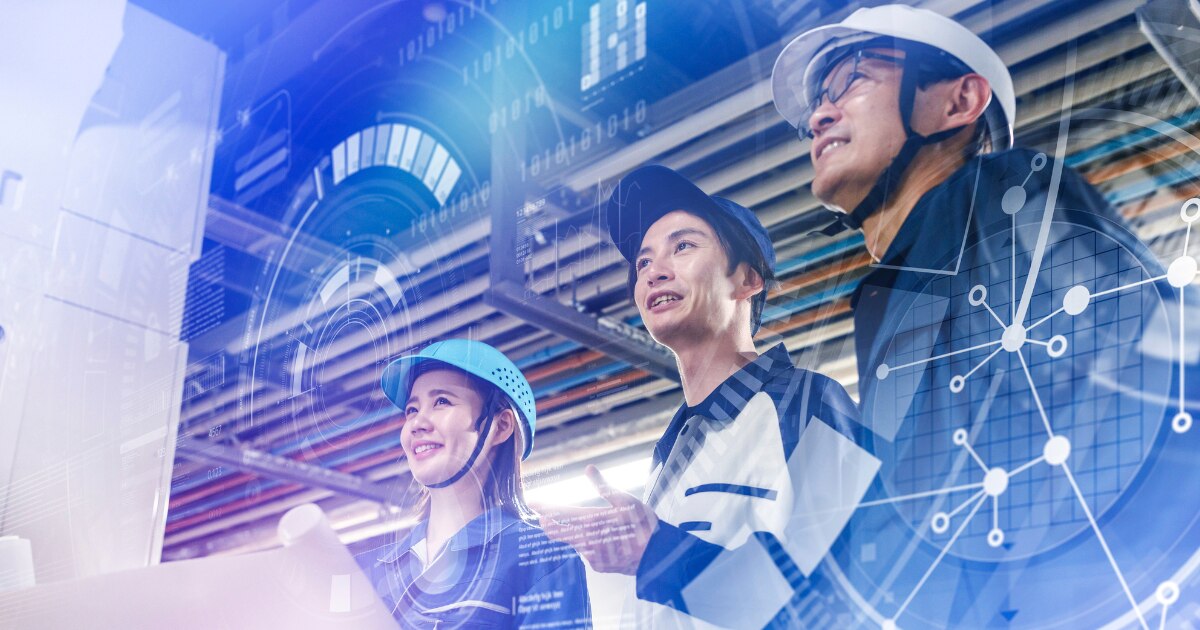
品質管理にAIを活用するメリット。製造現場での活用法や導入時の課題とは
AIは、人間が行ってきた知的活動をコンピュータによって再現する技術です。近年、製造業においてAIによるビッグデータ解析や生産の自動化が広がっており、その分野の一つに“品質管理”があります。
品質管理は製品の安全性・信頼性を確保するために欠かせない業務です。しかし、人に依存した検査では作業負荷がかかるほか、精度のばらつきや異常発生の見過ごしなどが発生しやすくなります。AIは、このような品質管理の問題を解決する方法として活用が期待されています。
この記事では、品質管理にAIを活用するメリットや製造現場での活用方法、AIを導入する際の課題について解説します。
なお、製造業における品質管理の課題についてはこちらの記事で詳しく解説しています。併せてご確認ください。
目次[非表示]
- 1.品質管理にAIを活用するメリット
- 2.製造現場の品質管理におけるAIの活用法
- 2.1.➀設備異常・不具合の予兆検知
- 2.2.②外観検査の自動化
- 2.3.③品質や設備故障の予測
- 2.4.④製品不良の要因分析
- 3.AIを用いた品質管理の課題
- 4.グレーボックスのAIモデルを構築するアットフィールズのアプローチ
- 5.製造現場でAIによる品質管理を運用した事例
- 6.まとめ
品質管理にAIを活用するメリット
AIは、膨大なデータに基づく情報の分類・予測や、高精度なデータ処理を行う“機械学習”や“ディープラーニング”の技術を備えています。
品質管理にAIを活用すると、製品の検査や生産工程の監視を自動化して、高精度かつ統一した基準で異常を検出できるようになります。
不良率の低減
目視による品質検査では、作業員の経験やスキルに依存するため、異常を判断する精度にばらつきが生じやすくなります。製品の欠陥を見逃したり、誤った判断をしたりしてヒューマンエラーが起きる可能性も考えられます。
AIを活用すると、センサー・カメラから取得した画像やデータを基に製品の異常を自動で検出することが可能です。生産ライン上の早い段階で異常を見つけて対処することで、不良率を低減できます。
品質の安定化
目視では判断が難しい軽微な異常や、音・においなどの感覚に依存しやすい検査などは、人によって判断の違いが生まれやすくなります。
AIは、個人の経験や感覚に頼ることなく学習した膨大なデータに基づいて統一した判断が行えます。これにより、検査の精度が高まり品質の安定化につなげられます。
作業員の省人化
従来の品質管理では、作業員が目視検査や記録を行うことから、生産ラインが増えるほど作業の負担が増える問題がありました。
生産ライン上の検査や記録作業をAIによって自動化することで、品質管理業務の省人化を図れます。別の業務に作業員のリソースを当てることにより、工場の人手不足解消や生産性の向上が期待できます。
製造現場の品質管理におけるAIの活用法
AIを活用すると、製造現場で発生する製品や設備機器のデータを蓄積・分析して品質管理の向上を図れます。
➀設備異常・不具合の予兆検知
AIが過去の稼働データを学習して正常値からの逸脱を判別することにより、設備異常・不具合の予兆を検知できます。異常・不具合が発生した環境やパターンを分析して、未知のトラブルを早期に検知することも可能です。
▼AIによる予兆検知を行う仕組み
- 振動・圧力・温度センサーなどで稼働データを収集する
- 稼働データの数値変動をリアルタイムで監視する
- 過去の正常値・異常値データから故障の兆候を判定するAIモデルを作成する
- 作成したAIモデルに基づいて異常・不具合を判定する
設備異常・不具合を検知した際に速やかにメンテナンスを行うことで、品質のばらつきや不良品の発生を未然に防げるようになります。また、設備停止による生産ロスや修理コストの削減にもつながります。
なお、予兆検知の仕組みを取り入れた保全方式に“予知保全”があります。詳しくはこちらの記事をご確認ください。
②外観検査の自動化
AIに良品・不良品の特徴を学習させて、外観検査を自動化する活用法があります。
▼AIによる外観検査の仕組み
画像引用元:経済産業省『AI導入ガイドブック 外観検査』
カメラで収集した製品データを画像認識技術によって分析することで、キズ・破損・汚れの付着などを判断して不良品を検出できます。
作業員が手作業・目視で行ってきた外観検査を自動化できると、検査精度のばらつきとヒューマンエラーを防ぐことが可能です。また、検査工程の時間・工数を削減して作業員の業務効率向上を図れます。
出典:経済産業省『AI導入ガイドブック 外観検査』
③品質や設備故障の予測
AIは、蓄積したデータの学習・分析によって未来の予測を行うことも可能です。製造現場での活用法として、品質や設備故障の予測が挙げられます。
▼原材料の品質予測
原材料や生産設備の設定状況、最終品質などの過去データをAIが学習して、製品の製造前に品質を予測できます。予測した品質結果を基に、原材料の配合割合や各工程の生産条件を調整することで、品質の安定化、不良率の低減を図れます。
▼設備の故障予測
過去に発生した故障データと設備の稼働データを分析して、故障が発生する可能性を予測することが可能です。故障予測の結果を基に部品交換や点検のリソースを確保することで、メンテナンスの最適化を図れます。
④製品不良の要因分析
設備機器から取得した稼働データと製品不良の情報をAIが分析して、要因と考えられる要素を特定することが可能です。
原材料・製造条件・工程などのあらゆるデータを基にAIが定量的な分析を行うことで、製品不良の相関性を明らかにできます。手動で要因分析を行う時間・工数を削減して、より効率的に改善のサイクルを回せるようになります。
また、製品不良のデータを蓄積してAIに学習させることにより、要因分析の精度向上を図れます。
AIを用いた品質管理の課題
AIによる品質管理を導入する際に直面する課題として、「処理の判断に至ったロジックや根拠が分からない」といった“ブラックボックス”の問題があります。
AIのブラックボックスによって生じる問題には、以下が挙げられます。
▼AIのブラックボックスによって生じる問題
- 透明性の欠如(内部の計算が複雑で結果に至るプロセスの説明ができない)
- 信頼性の問題(誤った予測に起因する誤った意思決定のリスクがある)
- ドメイン知識の欠如(現実の問題に対して適切な改善策を提案できない) など
AIがなぜ特定の判定・予測を行ったのか説明できないため、製造プロセスの問題や製品不良などに対する改善活動が誤った方向に進む可能性があります。
製造業では、プロセスの各ステップや結果を詳細に理解し、説明することが求められますが、AIはデータから自動的にパターンや関係性を学習するため、物理現象をモデル化することはありません。数値上、成立する条件のみが考慮され、物理現象の本質的な特性や制約は無視されます。そのため、AIが出した結果の説明ができないのです。
また、製造現場では必ず計測誤差が発生しますが、AIにおいてはこの誤差も含めてモデルリングするため、凡化性能(※)が確保されず実運用に使用できなくなります。
品質管理にAIを活用する際は、判定・予測結果を人間が解釈できるAIモデルの構築が必要です。ブラックボックスの欠点を補うためには、ホワイトボックス(物理モデル)を掛け合わせたアプローチによって、“グレーボックス”のAIモデルを構築することが有効です。
▼グレーボックスモデルのイメージ
※AIモデルの構築に使用した訓練データだけでなく、未知のデータに対しても精度の高い予測を行える性能。
グレーボックスのAIモデルを構築するアットフィールズのアプローチ
アットフィールズテクノロジーでは、物理現象の階層的な関係性を把握した上で、AIモデルを構築します。具体的には、製造現場の運用やプロセスフローを理解している技術者が、インプットするデータを選択したり、物理現象とマッチするようにデータを加工したりした上でAIモデルを構築します。こうすることで、現象を階層的にモデリングできるので、AIが判定した結果の根拠・ロジックを解釈できるモデル(グレーボックスモデル)を構築できます。
これにより、品質管理における改善活動の精度を高めることができます。
▼統計モデル×物理モデルによるAIモデル構築のイメージ
なお、近年ではAIが行った内部の計算を理解する“XAI(説明可能なAI)”という研究分野が注目されていますが、XAIが説明できるのは、変数間の数値上の関係性であり、変数間の物理的な関連性は明らかにできません。そのため、XAI技術を使用したとしてもやはり、製造業においてブラックボックスのAIモデルを実運用することは難しいと考えられます。
製造現場でAIによる品質管理を運用した事例
アットフィールズテクノロジーのアプローチ手法を用いて、製品加工結果の変化点をAIが自動検出する仕組みを構築した事例を紹介します。
▼課題
これまで製品の変化点や変化点と合致する部材・金型・治具の出来栄えの影響度を手動で解析しており、多大な工数と精度のばらつきが生じていました。
また、一般的なAIでは統計的な判断結果が示されるものの、正解率が低く改善アクションにつながらないといったブラックボックスの課題がありました。
▼実施内容
ツリー構造で事象を把握して、1階層(製品変化点)・2階層(部材の切り替わり)・3階層(部材出来栄えの影響度)をドリルダウン形式で検出できるようにグレーボックスによるAIモデルを実装しました。
【グレーボックスモデルを活用したAI自動検出】
▼成果
製品変化点をAIが自動検出することで早期の異常発見が可能になりました。また、変化点と一致する部材の特定や出来栄えとの紐づけによって要因を早期に特定することで、迅速な改善策を実現しました。
まとめ
この記事では、品質管理とAIについて以下の内容を解説しました。
- 品質管理にAIを活用するメリット
- 製造現場の品質管理におけるAIの活用法
- AIを用いた品質管理の課題
- グレーボックスのAIモデルを構築するアットフィールズのアプローチ
- 製造現場でAIによる品質管理を運用した事例
品質管理にAIを活用すると、膨大なデータに基づいて高精度な検査や設備故障の予兆検知、品質の予測などを行えるようになります。
ただし、ブラックボックスのAIモデルでは、判定に至ったロジックや根拠が不明なので、判定結果を改善活動に繋げることができなかったり、誤った意思決定をしてしまう可能性があります。
製造現場の品質管理に実用化できるAIモデルを構築するには、「なぜその結果が出たのか」を解釈できるグレーボックスモデルの実装がポイントです。
アットフィールズテクノロジーでは、現象をツリー構造で分解するアプローチによってグレーボックスモデルを構築することが可能です。品質管理の工数削減と安定化を図り、迅速な改善サイクルを実現します。
詳しくは、こちらの資料をご確認ください。