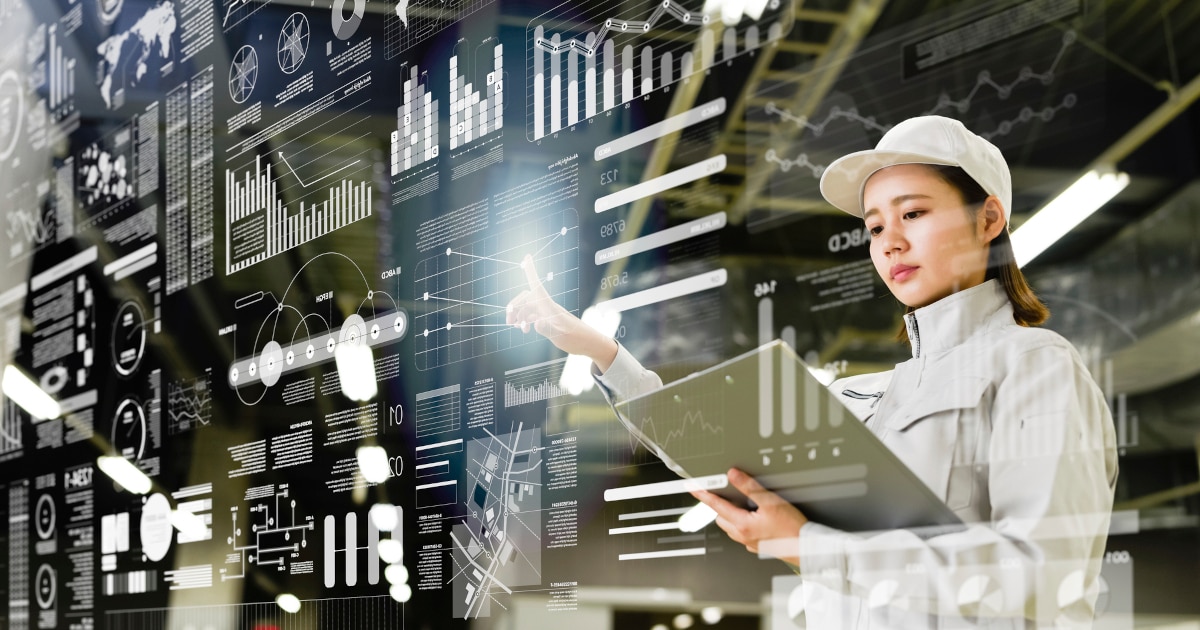
製造業のIoT化を成功させるには? スモールスタートによる導入がポイント
近年、製造業ではグローバル化による競争環境の激化やエネルギーコストの増大、就業者の高齢化による技術の継承などのさまざまな課題に直面しています。
このような課題に対応して持続的な事業の成長につなげるために、DX(デジタルトランスフォーメーション)による生産体制の変革が求められています。DXを推進するためのカギとなるのが、IoT(Internet of Things:モノのインターネット)の活用です。
IoTを活用することで、製造機械や設備などのあらゆるデータを収集・可視化したり、人の手で行ってきた作業を自動化したりできるようになります。ただし、IoTを導入すること自体が目的になってしまうと、製造現場の最適化にはつながらず、DXの実現には結びつきません。
「IoTを活用して何を実現したいのか」「導入によってどれくらいの費用対効果が期待できるのか」などを検討したうえで、戦略的にIoTの投資と導入を進めていくことが重要です。
この記事では、製造業にIoTを導入するメリットや課題、スモールスタートによる導入手順について解説します。
目次[非表示]
製造業にIoTを導入するメリット
製造業の現場にIoTを導入することで、次のメリットが期待できます。
▼メリット
- 生産性の向上
- 品質の安定化・向上
- 新たな製品・サービスの導入による付加価値の創出
製造現場にIoTを導入して、これまで人の手で行っていた生産ラインでの組み立てや巡回点検、品質チェックなどの作業を自動化・省力化することで、生産性の向上が期待できます。
製造機械・設備から収集した稼働データを分析すれば、非効率なフローの見直しやエネルギーの省力化などに役立てることも可能です。
また、作業を自動化してヒューマンエラーをなくしたり、製造機械・設備の稼働状況を監視して故障・トラブルを防いだりすることで、品質の安定化と向上につながると考えられます。
さらに、製造工程で取得したビッグデータは、以下のような新たな製品・サービスの導入に役立てられます。
▼ビッグデータを活用した新たな製品・サービスの例
- 納品した製品の稼働データを蓄積・監視して、メンテナンスの箇所や時期を提案するサービスを導入する
- 蓄積した製造データを基に今後の需要予測を行い、変種変量生産に対応する
顧客のニーズに対応した製品・サービスの導入は、自社工場の付加価値創出につながり、競争力の強化にも結びつくと考えられます。
IoTに関するよくあるお悩み
製造業でIoTの導入を進める際、次のような悩みに直面することがあります。
▼IoTに関するよくあるお悩み
- 費用対効果を算出できない、あるいは、その確実性が分からない
- データを収集したものの、その先で何をすればよいか分からない
- 新しい製造プロセスや作業方法になじめずに混乱が生じる可能性がある
近年のIoTトレンドや会社によるDX推進の影響から「とりあえずIoTを導入しなければ」という流れで導入すると、そこから先となるデータの利活用に行き詰まってしまうことがあります。
IoTには、インターネット環境の構築をはじめ、センサやシステムなどのIT機器の購入が必要になります。導入目的や課題を明らかにしないまま進めると、必要以上に規模を大きくしてしまい、余分なコストがかかるおそれがあるほか、製造現場の最適化までたどり着けない可能性があります。
また、IoTを導入するとこれまで人の手で行ってきた作業や製造プロセスが変化することから、現場に混乱が生じるリスクもあります。
コストの増加・損失や現場の混乱を防ぐには、費用対効果を算出しやすい小さな規模からスモールスタートして、効果検証と現場への定着化を行いながら計画的に進めていくことが重要です。
スモールスタートでIoTを導入する5つの手順
IoTの導入は、製造現場において“生産体制の改革を実現するための手段”となることを認識して、明確な目的・目標を決めて取り組む必要があります。
自社工場の課題や実現したいことを踏まえたうえで、IoT化する機械・設備、収集するデータを決めて導入を進めることがポイントです。大規模なシステムを一度に導入するのではなく、小規模な範囲からスモールスタートをすることで、投資を最小限に抑えて効果検証を行えます。
ここからは、たくさんのモノづくり現場で培ったアットフィールズ流のIoTの推進方法をお伝えします。
①現状課題と目指すゴールを明確化する
IoTによって解決したい製造工程の課題を洗い出して、どのようなゴールを目指すのかを明確にします。
課題とゴールを明確にしておくことで、収集・蓄積する製造データや必要なシステムなどが明らかになり、計画的な投資を行えるようになります。
▼課題とゴールの例
課題 |
ゴール |
|
例1 |
生産実績を手入力で管理しており、入力漏れやデータの紛失が発生している |
生産実績に関するデータを自動で収集して一元管理を行うことで、作業の効率化とヒューマンエラーの防止を図りたい |
例2 |
不具合発生の記録はあるものの、原因の特定が難しい |
不良データの収集と解析で原因の特定を可能にして、品質の安定化・向上につなげたい |
②既存の情報を基にIoTの優先度を見極める
製造現場で管理している紙媒体やExcelファイルなどにある情報を基に、現状課題の要因と影響度を分析して整理します。
生産性の向上や品質の安定化などの課題を踏まえて、費用対効果が期待できる製造工程にIoTを優先的に導入することで、目標の達成につながりやすくなるほか、失敗による投資コストの損失を防げます。
現状課題の要因と影響度を整理する際は、“パレート分析”を用いる方法があります。パレート分析では、各課題が製造工程全体のどの程度の割合を占めているかをグラフで示して、影響度が高い課題を把握することが可能です。
▼効果指標の要因別パレート分析のグラフ
なお、同時に紙媒体やExcelファイルで管理している情報をデータとして収集・管理する必要があるかどうかについても検討します。
③設備のデータ収集やアナログ業務をペーパーレス化する
IoTの導入をスモールスタートする一歩となる取り組みが、設備1台からのデータ収集や紙媒体およびExcelファイルで管理している業務のペーパーレス化です。
生産設備のデータ収集から活用を最小限の投資で行うためのポイントには、以下が挙げられます。
▼最小限の投資で設備データの収集から活用を行うポイント
- ステップ2で判断した最も優先度の高い工程や要因から実施する
- 設備1台からでもスタートできる収集システムを選択する
- 各社製PLCやアナログデータ出力など、既存資産に対応できる収集システムを選択する
また、代表的なアナログ業務のペーパーレス化には、以下が挙げられます。
▼ペーパーレス化の例
- 品質不良・不具合発生の記録を紙媒体からタブレット入力などの活用に変更してデジタル化する
- 生産・作業実績を、設備またはバーコードリーダーなどから情報を抽出して、生産管理システムに転記する
- 設備点検やメンテナンスの帳票は、カメラによる画像認識やタブレット入力などを活用してデジタル化する
設備データ収集及びペーパーレスに取り組む際は、どちらも製造への課題が大きく重要な工程から着手することがポイントです。
④PDCAを回しながら、工場全体へと展開する
PDCAとは、Plan(計画)・Do(実行)・Check(評価)・Action(改善)の工程を繰り返しながら改善を図るフレームワークのことです。
IoTの導入によって製造機械・設備の稼働データを収集・蓄積したあとは、稼働率や不良率の分析によって実効性を検証して、問題の解消と改善を図ります。
一つひとつの製造工程で効果検証を行いながら、ほかの機械・設備やラインへとIoTを展開していくことで、コストの増加や実証段階での失敗を防げます。
⑤自律的な稼働体制へと発展させる
DXを推進して生産体制の変革を図るには、IoTを工場全体へと浸透させて自律的な稼働ができる体制へと発展させることが重要です。
故障や不具合の予兆監視、製造工程の自動制御などを実現することで、省人化・省力化によるコスト削減および品質の安定化につながり、生産性の向上を図れます。
▼自律的な稼働体制の構築例
- 稼働データの常時監視を行い、不具合の予兆や異常を自動検知して管理者へ通知する
- 生産ラインの品質チェックを自動化して、AIによる不良品の判定を行う
- 製造現場の利用状況や温度データを取得して、照明・空調を自動で制御する
スモールスタートによるIoTの導入事例
ここからは、スモールスタートでIoTを導入するにあたって、製品の不具合管理をペーパーレス化した事例を紹介します。
▼課題
これまでは紙媒体で不具合の発生状況を記録しており、管理者が記録表を集めて不定期に表計算ソフトへと転記をしていました。
しかし、現場と管理者へのタイムリーな情報共有が難しく、調査部門や品質部門への水平展開ができないことから再発防止の対策を十分に行えていませんでした。
▼取り組み
不具合に関する情報をWebで入力・参照できるシステムをスクラッチ開発で構築して、リアルタイムな情報共有を行える環境を整備しました。
システムの構築イメージ
▼効果
不具合が発生した際に、システムを介して原因調査や対策を行う部門へとエスカレーションを行い、関係者への水平展開ができるようになりました。また、不具合の事象や実施した対策についてデータベースで一元管理することで、分析による改善活動を行えるようになりました。
まとめ
この記事では、製造業のIoT化について以下の内容を解説しました。
- 製造業にIoTを導入するメリット
- IoTに関するよくあるお悩み
- スモールスタートでIoTを導入する5つの手順
製造現場にIoTを導入すると、生産性の向上や品質の安定化・向上、新たな製品・サービスの導入による付加価値の創出などのさまざまなメリットが期待できます。
ただし、環境構築やIT機器の導入などにはコストが発生するほか、大規模な範囲で一度にIoTを導入すると現場に混乱が生じるおそれがあります。コストの増加や現場の混乱を防ぐには、スモールスタートでの導入がカギとなります。
目的・目標を明確にしたうえで、課題が大きい製造工程から小規模でIoTを導入することで、効果検証と現場への定着化を行いながら計画的に進められるようになり、失敗のリスクを抑えられます。
『アットフィールズテクノロジー』では、製造現場の稼働データを収集して一元管理ができるツール『@FieldEye-Edge』を提供しています。蓄積したビッグデータの解析や監視などにも対応しており、品質ロスの低減や製造フローの改善などに役立てられます。
サービスに関する詳しい資料は、こちらからダウンロードしていただけます。ぜひご確認ください。